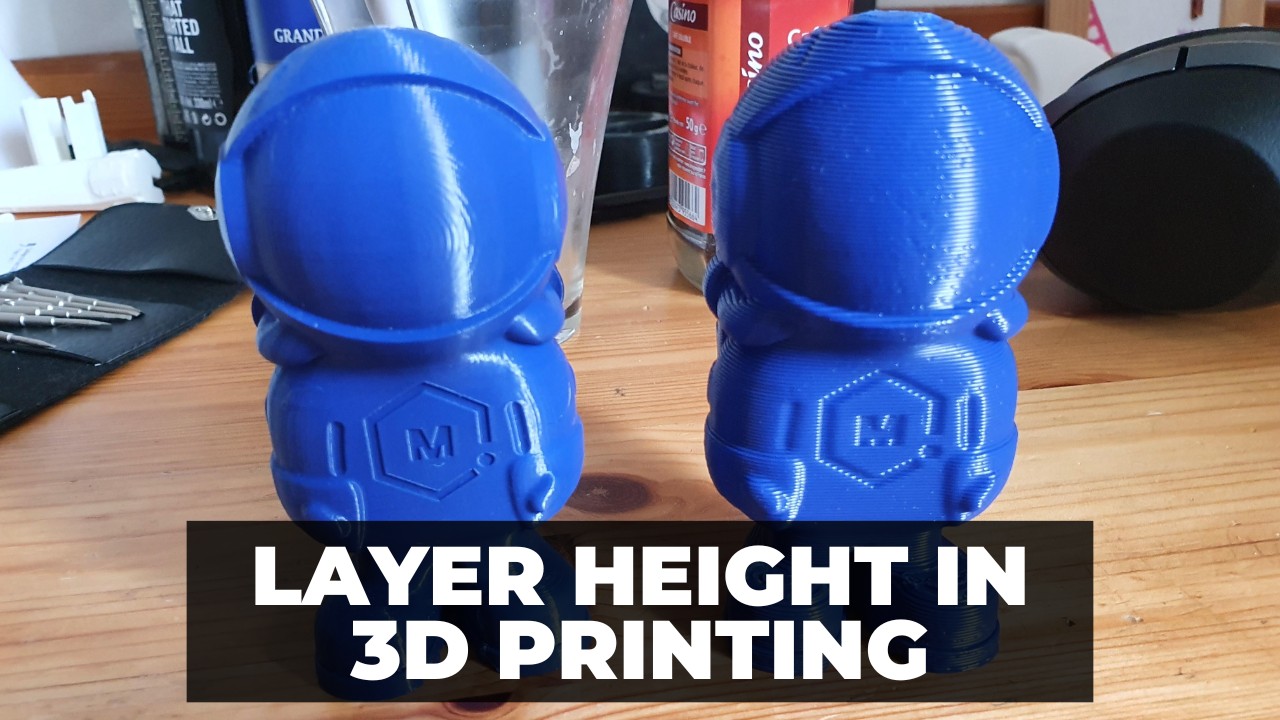
Layer Height In 3D Printing: Why It Matters & Best Layer Heights For Every Filament & Use
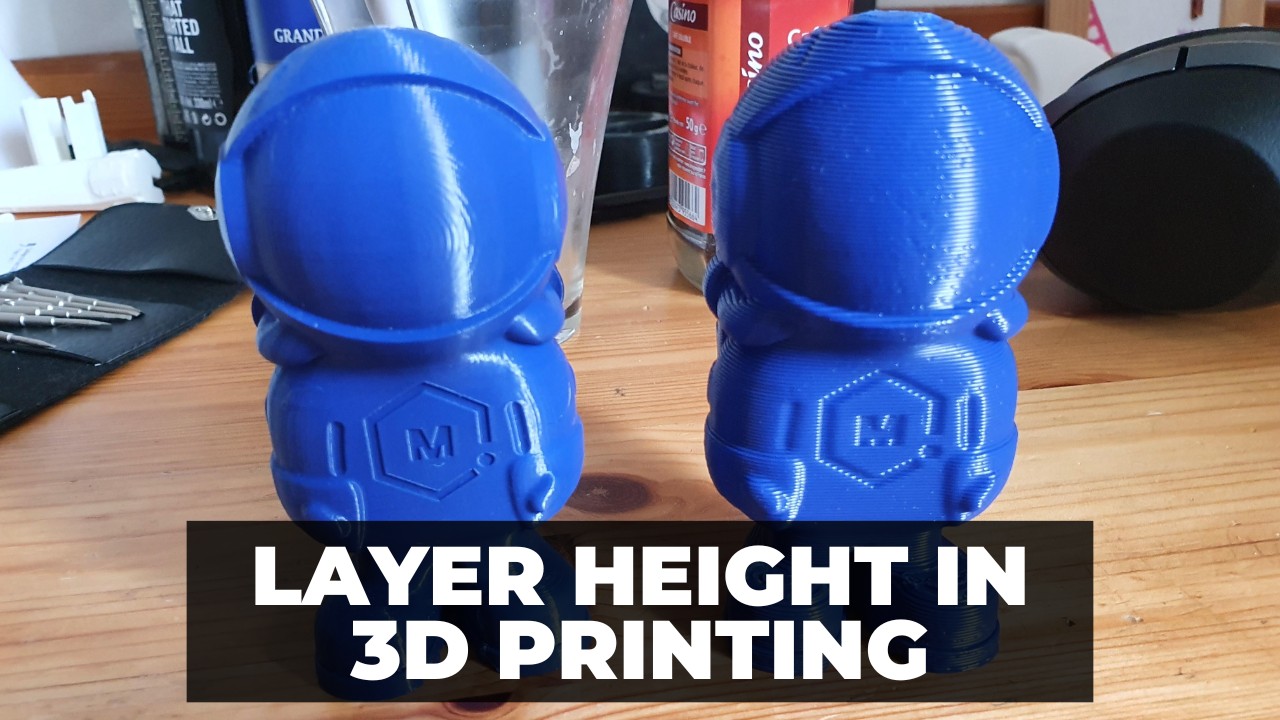
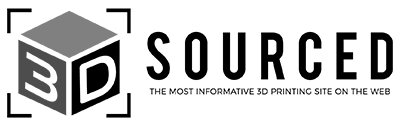
At 3DSourced we’ve covered everything 3D printing and 3D since 2017. Our team has interviewed the most innovative 3D printing experts, tested and reviewed more than 20 of the most popular 3D printers and 3D scanners to give our honest recommendations, and written more than 500 3D printing guides over the last 5 years.
With 3D printing, there are dozens of different parameters that you can play with. One that is constantly discussed is layer height. People want to know the best 3D printing layer height, but why does that even matter?
In this guide, we’ll teach you everything you need to know about the layer height in 3D printing. We’ll discuss what it is, how it works, why it matters, and what a huge impact it has on your final parts.
What Does Layer Height Mean in 3D Printing?
Every layer your 3D printer deposits has a certain height. Layer height simply refers to how tall each layer is — it’s measured in either millimeters or microns, but most of the industry uses millimeters. Smaller layer heights result in better surface finish, whereas larger layer heights create a boxier look.
If your layer height is 0.15mm, then the printer will deposit a bead of plastic that’s 0.15mm thick, and the head will move up 0.15mm between each layer.
If you were to build a brick building, you would stack up bricks along the perimeter, one layer at a time. After enough layers are stacked up, you’re left with a completed building. If you use taller bricks, then you’ll be done in fewer layers, and you’ll get the job done faster.
The same theory is at play in 3D printing.
When a 3D printer makes a part, it’s using a bead of molten plastic and tracing the part’s outline and internals. The bead will quickly cool and solidify. While this is happening, the 3D printer’s extruder moves up a little bit in the Z direction, and starts laying down the next layer.
This process continues until you have a finished part — just like how the brick building was built.
In this case, the thickness of the molten plastic bead will determine how many layers the printer needs to do.
This is layer height, in a nutshell.
How the Layer Height Affects Your 3D Prints
How To Change the Layer Height
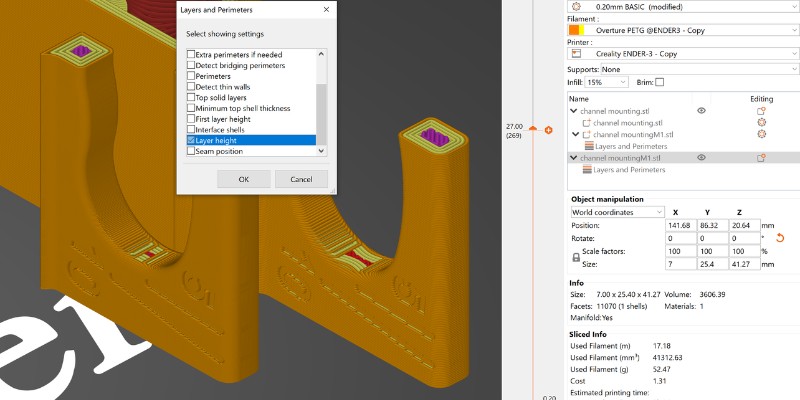
After you draw a 3D part, you’ll load it into a slicer. This is software that translates a solid part into code that your 3D printer can understand. The slicer will ask you for dozens of parameters and write thousands of lines of code, then it gives everything to the printer.
Within those parameters, one of the bigger ones is the layer height.
For slicers like Cura, layer height will be changed directly through the software. The changes to the software will be embedded in the code that’s later given to the printer, so the printer will physically print at whatever layer you told it to.
However, your nozzle’s size will limit your layer height. With a 0.25mm nozzle, you can’t print any layer thicker than 0.19mm. Let’s explain why that’s the case.
Nozzle Diameter and Layer Height
Every nozzle you install has a little hole in the center that goes to the tip of the nozzle. It’s called a bore, and this is where the molten plastic gets pushed out.
The bore has a very specific diameter dimension. If you install a 0.40mm nozzle, that means that the hole measures 0.40mm across (as a diameter).
The rule of thumb is that a nozzle can handle a layer height between 25% and 75% of its diameter. Using that math on a 0.10mm diameter nozzle means that you can print a layer height between 0.025mm and 0.075mm.
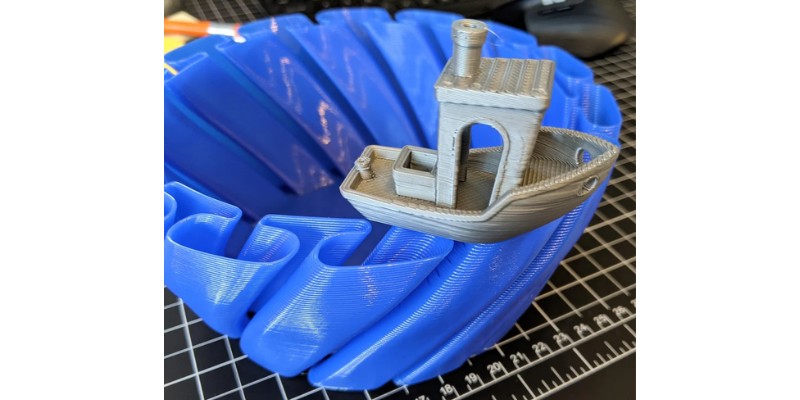
If the layer is too thin, the nozzle can’t appropriately control the flow — this leads to a reduced part quality, inconsistent layers, and poor aesthetics. If it’s too thick, then there’s not enough space in the bore to reliably push out the material.
Read more: nozzle size 3D printing guide
Range of Layer Heights to Consider
The perfect layer height for any nozzle is 50% of its diameter. A later table will show you the lowest and highest acceptable height, depending on your nozzle size.
You’ll typically find nozzles between 0.10mm and 2.0mm. Using the 25% to 75% rule, that means that the full range of layer heights on a traditional FDM 3D printer is between 0.025mm and 1.50mm.
Though, in practice, most people don’t use nozzles over 0.60mm unless they have a specific need to expedite low-resolution parts.
Within this range, any layer 0.15mm or under can be considered a “small” layer height. This requires a 0.25mm nozzle, which is certainly smaller than most other options on the market.
NOZZLE SIZE (mm) | LOWEST LAYER HEIGHT (mm) | HIGHEST LAYER HEIGHT (mm) |
---|---|---|
Layer height for 0.1mm nozzle | 0.03* | 0.08 |
Layer height for 0.25mm nozzle | 0.06 | 0.19 |
Layer height for 0.4mm nozzle | 0.10 | 0.30 |
Layer height for 0.6mm nozzle | 0.15 | 0.45 |
Layer height for 0.8mm nozzle | 0.20 | 0.60 |
Layer height for 1.0mm nozzle | 0.25 | 0.75 |
*-Most consumer-grade FDM printers will struggle to hit 0.03mm without serious reliability issues. The motors, belts, and extruder heads aren’t precise enough to use such a thin layer of material. Layers will smear, lift, and have trouble adhering if you go this low.
With this context, let’s discuss how the layer height changes your print.
The Impact of Layer Height on Your Print
Even though the difference between 0.10mm and 0.30mm seems so small, it’s very important. This tiny adjustment to your layer height can have huge effects on your final print.
Here are some major impacts that the height has on your finished part:
Print Time
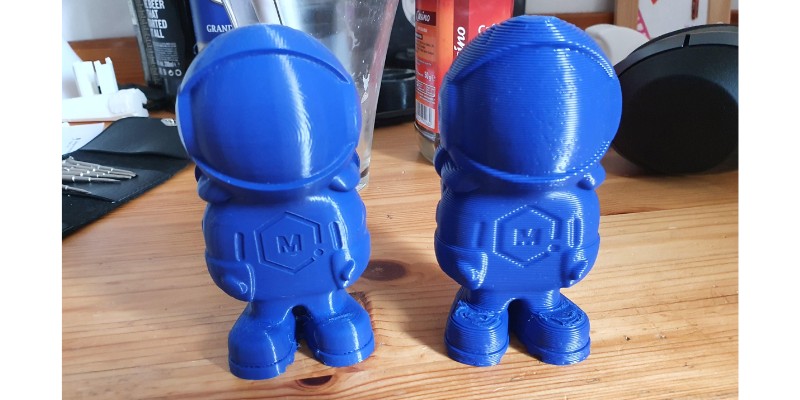
Perhaps the biggest impact is the final print time. The layer height will determine how many layers need to be printed in total — with a smaller height, more layers will need to be laid down, so it will take longer to finish the part.
The printer will take the same amount of time to lay down each layer (as long as the print speed is the same), it’s just a matter of how many layers it has to do before the part is done.
Opting for a very small layer height will typically multiply the total print time. Going from a 0.50mm layer height to a 0.10mm layer height will turn a 2-hour print into a 10-hour print.
Final Resolution

The resolution of your part is how smooth it looks. A low-resolution part will look boxier, edges won’t be rounded, and you’ll notice each layer. This is more common when you use thicker layer heights.
If you’re making a part for aesthetic reasons, it’s better to go with smaller layer heights. You sacrifice the total print time in exchange for smoother-looking parts.
Part Strength

People typically don’t think of strength when they consider 3D printed parts, but parts can be pretty sturdy. They’ll never outperform metal parts, but there are countless applications where 3D printed plastic parts can take an impressive amount of force — like 3D printed wrenches or door handles.
Read more: 3D print strength – PLA, ABS and more compared
In cases like these, you need to know which layer height gives you the strongest 3D prints. Typically, 0.15mm is the strongest option when it comes to layer height. It hits the sweet spot between too thick and too thin.
If you go too thick, then the part will easily separate between layers. With some prints, you can physically tear the print apart between these thick layers.
Too thin isn’t always a bad thing, but it can lead to inconsistencies in the print. Going down to a 0.05mm or 0.10mm layer height will reduce your strength a little.
Ability to Create Round Surfaces

Going hand-in-hand with the idea of resolution, making rounded surfaces depends heavily on your layer height.
It’s the same as picking what size paintbrush you want to use for your art — thicker paintbrushes will fill the canvas quicker, but you’ll lose out on details and specific geometries.
With a thick layer height, your rounded features will have square steps on them. Holes might appear oblong, and circles won’t be symmetric.
Print Stability
Layer height also affects your print’s stability. If you’re running at high lift speeds and quick retraction rates, a thicker layer height like 0.40mm can compound issues that you might see on your print.
Specifically, it’s more likely that you’ll have layer separation, or the print will shift midway up.
With thicker layer heights, you can also experience delamination. This is when your filament doesn’t cool, and sticks to the previous layer. Instead, it protrudes up a little bit. The printer will keep going, and you’ll be left with gaps and cracks in your finished part.
The Bottom Line: It’s a Trade-Off Between Layer Height and Speed
By now, you might have noticed that layer height is just one big trade-off. Before every print, you need to ask yourself which is more important: aesthetics, or print time.
Larger layer heights will churn out prints faster, but at a lower resolution. You might get blockier-looking parts, but you’ll get them in a fraction of the time.
On the flip side, you’ll get much smoother and stronger parts if you dial down the layer height and opt for thinner layers.
Material Choice Can Change the Ideal Layer Height
There’s another caveat when it comes to layer height: you need to consider the material you’re printing with.
Some materials are more difficult to work with on standard FDM printers. Going for a much taller or shorter layer will make problems even worse.
Let’s look at three of the most common 3D printing materials and discuss the best printing layer heights for each.
What Is a Good Layer Height for PLA?
PLA is one of the more common plastics, and it’s generally easier to work with. You can print PLA at a wide range of heights, but most people will stick to 0.15mm or 0.20mm with a 0.40mm nozzle.
At this height, you have a good balance between strength, speed, and resolution.
Since PLA is so easy to work with, you can also print thicker layers, but you’ll sacrifice resolution and strength. Still, the material won’t necessarily limit your layer height.
Read more: the best PLA filament

What Is a Good Layer Height for ABS?
With ABS, you want to be more conservative with your layer height. Try not to print under 0.20mm, and the best layer height for ABS is closer to 0.30mm (if the resolution isn’t the main focus).
ABS is a little more stubborn and trickier to work with. A common issue is just getting the first layer to stick. On top of that, ABS prints at a much higher temperature. If the height is too small, then you can smear the previous layer before it’s fully cooled.
Read more: the best ABS filament
What Is a Good Layer Height for Nylon?
It’s best to stick to a layer height between 0.20mm and 0.40mm.
Printing with Nylon can be even more troublesome than ABS. You want to make sure you turn the speed down and turn your fans up, so the Nylon can cool between layers. It also requires a high hotend temperature and bed temperature just to stick and avoid warping.
Read more: the best Nylon filament

Each 3D Printer Is a Little Different
Looking into the mechanics at play with a 3D printer, there’s even more going on that affects the perfect layer height.
If a printer has high-resolution stepper motors and impressive drivers, you can get away with thinner or thicker layer heights.
Best Layer Height for Creality Ender 3
A printer like an Ender 3 has pretty good motors, but the belts can be a little sloppy during installation. As a result, the best layer height for an Ender 3 is between 0.15mm and 0.30mm.
Whenever you get a new machine, you should start by trialing some layer heights and seeing which works best.
Picking the Best Layer Height
Let’s say you’re firing up a 3D printer for the first time, what’s a good layer height for general 3D printing, and how do you pick the right layer height?
You have two different paths: You can either stick to the industry norms, or you can do some trial and error.
Going through multiple attempts and failing will teach you a ton about the connection between your machine, material, and layer height. Try printing a 3DBenchy at a variety of layer heights to see the difference for yourself.
If you want to stick to the industry norms, then consider previous sections where we outlined standard print heights.
For PLA, set your slicer and printer to 0.20mm and use a 0.40mm nozzle — this setup can be kept for a majority of your prints, unless you need to optimize the aesthetics or print time.
Some people set a time-tested layer height for their prints and never change it. If you find something that works, then stick with it.
Conclusion
Going for taller layer heights will finish your print faster, but you’ll have a weaker and lower-resolution part. Thinner heights take longer, but they result in parts that look much neater. Understanding the balance is important for your success as a 3D printer. Start with our suggestions, then go through some trial and error to learn more about the best 3D printing layer height for your 3D printer.
Related articles:
- Common Causes of Extruder Clicking/Slipping And How To Solve It
- Precision In Your 3D Prints: Explaining Dimensional Accuracy
- Troubleshoot Guide: Filament Grinding
- Are Your 3D Printing Layers Shifting? Read Our Comprehensive Guide
- How To Troubleshoot 3D Print First Layer Problems
- Help! My 3D Printer Is Too Hot / Overheating
- Layer lines in 3D printing: how to eliminate layer lines