
Top 3 DIY Filament Dry Box Projects You Can Make at Home

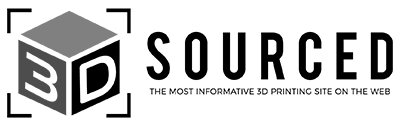
At 3DSourced we’ve covered everything 3D printing and 3D since 2017. Our team has interviewed the most innovative 3D printing experts, tested and reviewed more than 20 of the most popular 3D printers and 3D scanners to give our honest recommendations, and written more than 500 3D printing guides over the last 5 years.
Is wet filament spoiling your prints? Do you live in a particularly humid area? A DIY filament dry box might be just what you need to solve these pesky material woes.
Though settings, mods, and 3D printer specifications dominate the conversation around how to create the best possible prints, filament also plays a huge part. Keeping your filament moisture-free and in pristine condition can make all the difference to print quality.
On this page, we’ll show how to do just that with a guide to piecing together a DIY filament dry box to keep even the most moisture-absorbing filament bone dry. We’ve handpicked what we consider to be three of the best projects around.
They’re affordable, easy to make, and excel at keeping your filament moisture-free.
Air-Tight Plastic Container DIY Filament Dry Box
- Price: As low as $15.00
- Assembly Time: 30 mins to an hour
- Required Materials: Storage container, rod/pipe, hardware (bearings, cable glands, tube pushes, screws, nuts, bolts), PTFE tubing, 3D printed parts, desiccant/silica gel packs.
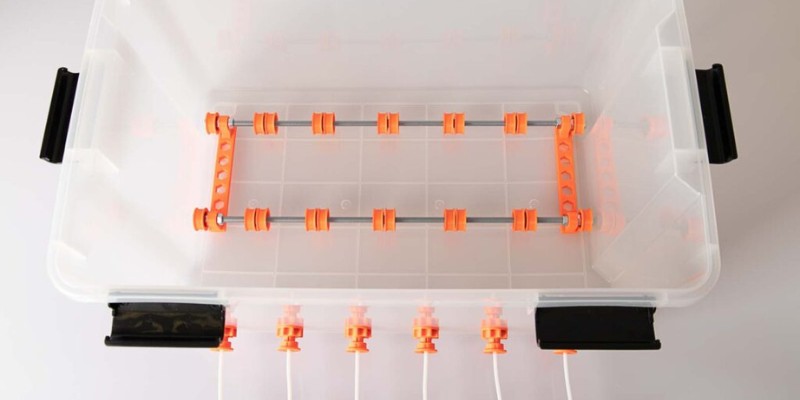
First, the air-tight container – a classic DIY filament box option, designed to dispense material without removing it from the box and act as a storage container when not in use. It keeps the filament away from moisture while also protecting it from dust.
To complete this project, you’ll need a plastic storage container with a cover – make sure it’s large enough to house a filament spool or several if you want to store multiple.
Next, you’ll need a rod or pipe with a length that corresponds to the width of the container to support the spool but also allows it to spin freely.
Other projects use variations on this, such as a series of bearings mounted on a bracket sitting at the bottom of the container to rotate the spools.
Depending on the project, you’ll need a selection of 3D printed parts to support the rod, bearings, other hardware, and PTFE tubing. After drilling feeder holes into the container, route the filament through the PTFE tube all the way to the printer’s extruder.
Some designs also incorporate more complex feeder hole plugs to keep the filament end dry when not attached to the printer, especially useful if you go for a multiple spool DIY dry box for filament.
Hygrometer humidity and temperature sensors are also a popular add-on to quickly check the state of your filament.
Although lidded containers protect against moisture, they aren’t completely air-tight. Many projects also recommend laying down desiccant or silica gel packs at the bottom of the container to absorb moisture passively.
We recommend reusable silica beads, as you can dry them out and reuse them multiple times. They also tend to change color as they absorb moisture – a helpful indicator that they need replacing/drying out.
Below, you’ll find a list of links to various air-tight plastic container DIY filament dry box projects we recommend:
3D Printed DIY Filament Dry Box
- Price: $80.00 – $100.00
- Assembly Time: 50 hours to 3D print parts, one to two hours for assembly
- Required Materials: bearings, hygrometer, battery, magnet, nuts, screws, PETG panels, 750 g filament for 3D printed parts, silica gel, PTFE tubing.
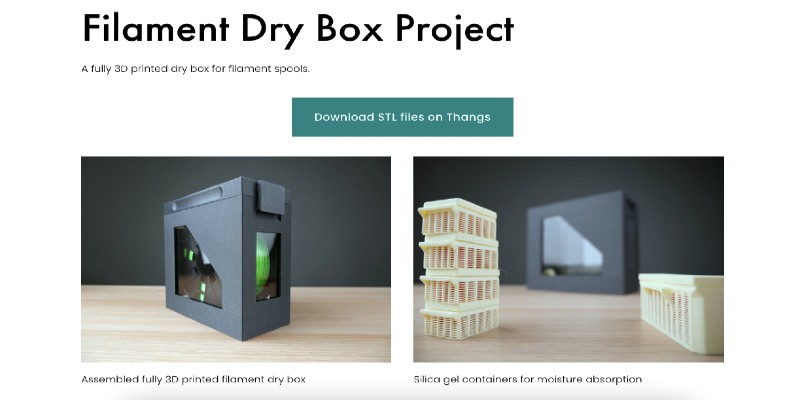
An alternative to a pre-bought container is to make a 3D printed dry box yourself and use bearings, PTFE tubing, battery, magnet, and other hardware to complete the project.
Though there are other designs, we’ll highlight Mihai Design’s dry box project because it pushes the boat out with sophisticated features and looks superb.
Notable features include a latched opening at the top to load and unload filament, an integrated hygrometer, and optional PTFE panel windows to track how much filament you have left.
Elsewhere, the design includes a knob filament rewind system, an air-tight filament gateway with a locking mechanism, and 3D printed silica gel cages with their purpose compartments within the case.
As most of the case is 3D printed (you’ll need 750 g of filament), completing the project takes more time, and the extra features require additional parts you wouldn’t need with a more straightforward design.
Nevertheless, it’s well worth the extra investment and time for just how well it protects your filament from moisture.
The only downside is that the design is only suitable for a single 1 kg filament spool.
The assembly process goes as follows:
- Build and attach the rewind knob to the case.
- Install the double filament gear.
- Install lower rollers at the bottom of the case.
- Assemble and attach the filament exit valve.
- Install lid rollers.
- Install hinges and hygrometer.
- Fix the PTFE panel windows to the case.
- Fill up and install the silica cages.
- Install tubing.
For more details, check out Mihai Designs’ dedicated YouTube video series.
Heated DIY Filament Dry Box
- Price: As low as $20.00
- Assembly Time: 30 mins to an hour
- Required Materials: Heating mat, temperature and humidity sensor, cable glands, 3D printed parts, threaded rod, nuts, desiccant.

Finally, by incorporating a heating element, you can make a DIY filament dry box that also doubles as a DIY filament dryer.
The process follows the steps to build a classic air-tight container dry box, but you have to buy and install a heater, and usually a compact mat. Otherwise, you’ll need similar off-the-shelf and various 3D printed parts.
To keep costs down, we recommended RichRap’s super thrifty DIY heated dry box project, which, according to their estimate, shouldn’t cost any more than $20.
Of course, part costs may vary on availability and pricing in your area, but the project invariably comes back cheaper than a store-bought filament dryer.
For the project, you’ll need a cheap heated mat (eBay is a good source of cheap heaters), a low-cost hygrometer, tubing, cable glands to supply power and for the feeder holes, a threaded rod, nuts, desiccant, and 3D printed spool holder/base.
It’s essential to buy a container large enough to fit the spool. We also recommended one with chunky closing latches to ensure as tight a seal as possible.
The heater sits on the grooves of the 3D printed base to ensure efficient heat transfer to the filament.
Punch through a feeder hole or several if you’re using a large container along with an exit hole for the heater power cable, install the glands, then the tubing, and attach the hygrometer to the printed frame – you’re ready to go.
For our money, RichRap’s project is the easiest to make by quite a stretch, so it comes highly recommended for those that need a dry box up and running as soon as possible.
RichRap also offers a few add-ons, including an optional lid seal to help further keep moisture away from the filament and a nifty spool check sensor.
Advantages of a DIY Filament Dry Box
Low Cost
With all the parts considered, a completed DIY filament dry box project costs considerably less than a manufactured solution.
Most achieve this with results that only trail slightly behind buyable alternatives – they efficiently keep filament dry, which leads to smoother and higher quality prints.
The trade-off is that this is a hands-on project, meaning you don’t get the convenience of an off-the-shelf, ready-to-go manufactured solution.
Space for Multiple Spools
Unlike most manufactured filament dry box products, you can customize a DIY project to house multiple filament spools instead of just one.
You can have various colors/types available, dry, and ready to print at any moment – a benefit for heavy users who jump between materials. There’s no upper limit on how many spools you can have other than finding a large enough container.
Customizable
Do you need the dry box to double as a filament dryer box? Install a heater. Do you want to store different filament spool sizes and 1.75 mm/2.85 mm diameters? No issue here; simply use a larger storage container. Humidity sensor? No problem.
The point is that a DIY filament dry box is customizable.
You can adapt it to your needs while still keeping costs down, unlike buyable boxes with their fixed designs, specifications, and higher price tag. In the case of a 3D printed box, you can even dive into CAD software to adapt it even further to your particular needs.
Filaments That Benefit Most From a Dry Box
All 3D printing filament types are hygroscopic to a certain degree.
In other words, they naturally absorb moisture and humidity present in the air. It’s, therefore, recommended to properly store all types of materials in a dry box or vacuum-sealed bag when not in use.
However, there are a few moisture fiends, such as flexibles like PETG and TPU, that suck in humidity like nobody’s business and can cause printing problems even when exposed for a short duration.
These benefit most from a DIY dry box for filament. Proper storage of these should be prioritized over materials like PLA, which can happily sit out for a fair few hours without absorbing enough moisture to cause issues.
Effectiveness Compared to Manufactured Filament Storage Solutions
For all their cost-cutting appeal and the sheer satisfaction that accompanies a homemade solution, DIY filament dry boxes don’t protect your filament against moisture as well as manufactured solutions.
While the performance gap isn’t an ocean, it still exists.
For those who don’t want the fuss of frequently replacing desiccants or who don’t want to make a dry box, paying extra for a professional product might be a better option.
For more details on your options, check out our guide to the best filament storage containers.
FAQs
How do you make a filament dry storage box?
You can make a DIY dry box for filament using a modified manufactured airtight container such as the Ikea Samla or from 3D printed parts.
The top aim is to ensure the container is sealed and doesn’t allow much moisture to creep in, even in very humid environments.
Aside from the container, you’ll need a spinning rod to support the filament spool, drill feeder holes, and install tubing to feed the filament to your printer.
With these basics ticked off, you can customize the box as much as you want by adding, for example, a humidity sensor, a heater, or silica gel sacs to improve moisture absorption.
If you are interested in our other filament guides, check out:
- Best filament dryers
- How to dry wet filament
- The best Nylon 3D printers
- The best TPU filaments (and TPE, flexibles)
- Our complete guide to ABS filament
- Our complete guide to PLA filament
- Our comparison of PLA vs ABS
- The best 3D printers buyer’s guide
- The top 10 FDM 3D printers
Other projects articles: