
Solid metal 3D printing can only be done on metal 3D printers… unless you use metal filaments. With metal-filled filaments you can print heavy, metallic, and even magnetic objects — all on a desktop 3D printer.
What are Metal Filaments?
Rather than being pure metal, metal filaments instead contain a percentage of metal powder within a standard plastic filament. Although any polymer can be used, PLA is almost always used as the suspension.

Metal Filaments Vs Metal Color Filaments
Ensure that the filament you’re purchasing actually contains metal. True metal filaments will be described as “metal-filled,” or “composites,” and will disclose their metal content percentage.
If your purchase doesn’t contain this wording, then you may instead be purchasing a spool of polymer filament with a metallic color.
A Brief History of Metal Filaments
Metal 3D printing could be said to have begun with the development of Direct Metal Laser Sintering (DMLS) in 1994. This process fuses metal powders together, creating solid metal objects.

Despite advances in DMLS since, metal 3D printing remains inaccessible, chiefly because it requires large and expensive industrial 3D printers to produce.
This is where metal filaments offer an alternative. Although they don’t possess all the properties of pure metal, they can extrude through a conventional Fused Deposition Modeling (FDM) 3D printer. Without the need to purchase a DMLS machine, metal filaments are a vastly cheaper and therefore more accessible way to produce metallic objects.
Properties of Metal Filaments
The properties of your metal filament will depend on the type of metal powder used, and how much of it is present within your spool. Despite this, there are some properties present in all metal filaments.
All metals add a color to their spool, adding a metallic finish to your prints in a similar way to metallic car paints.
Metal filaments are significantly heavier than polymer materials. Although not as heavy as pure metal, metal-filled filament parts feel more solid than polymer ones. However, they are far more brittle.
Although metal filaments can be used in the same way as polymer filaments, their fragility makes them unsuitable for producing objects that require a high degree of strength.

Metal filament 3D printing parameters & temperatures
With the exception of part-cooling fans, which are required, metal filaments do not need any additional equipment for 3D printing. However, some optional hardware and considerations may produce better results, and make life a little easier.
- Metal filament extruder temperature: typically ranges between 190⁰C-220⁰C. However, check your filament for the specific temperature to use.
- Heated bed: optional but recommended. If used, it should be set to 45⁰C-60⁰C.
- A hardened steel nozzle is recommended, as the abrasiveness of metal filaments will quickly degrade brass nozzles.
- Build surface: PEI sheets or painters tape are recommended.
- Ensure that the filament has as straight a path as possible between the spool and extruder. As metal filaments are brittle, sharp bends or curves could cause it to crack or even snap while printing.
Types of Metal Filaments
Although any metal can be used to create metal filaments, the three most common used are bronze, stainless steel, and copper.
As with all metal filaments, color and finish are the main factors when purchasing. However, these three metals also have different properties, and varying applications.
Bronze & Copper 3D printer filaments
Bronze and copper are commonly used 3D print sculptures and museum replicas. Copper’s finish can give modern sculptures a rustic appearance, while bronze 3D prints imitate the appearance of genuine ancient metal, something that steel can’t achieve without paint.
They are further unique from stainless steel in that they can corrode. This brings with it the challenge (or opportunity) of dealing with patina formation.
When oxidized these metals will develop a colored outer layer known as a patina. Interestingly, this same process turned the Statue of Liberty from its original gold to its now famous green.
For those keen to work with this corrosion and create aged-looking models, patinas represent an opportunity to print objects that can permanently change colour over time.
In an open environment, a patina can take 20 years to fully develop. However, certain techniques can artificially accelerate this process. For example, submerging copper or bronze in a solution of vinegar can begin to show the effect in just an hour!
However, this could also be a headache for those looking to preserve the metal’s original color, with the patina having to be scrubbed off regularly. It is possible to prevent patinas from forming by covering your print with wax, but this also means that your final print will have a waxy finish rather than a metallic one.

Stainless steel filaments
In addition to being immune from both rust and corrosion, stainless steel sets itself apart as the only magnetic material of the three.
The strength of the print’s magnetism is dependent on its metal concentration, with high concentrations possessing a magnetism indiscernible from pure steel.
Although brittleness means that steel filament can’t be used in stress-bearing objects like screws or paper clips, its magnetism gives designers a whole new dimension to work with… even if it is just to 3D print fridge magnets.
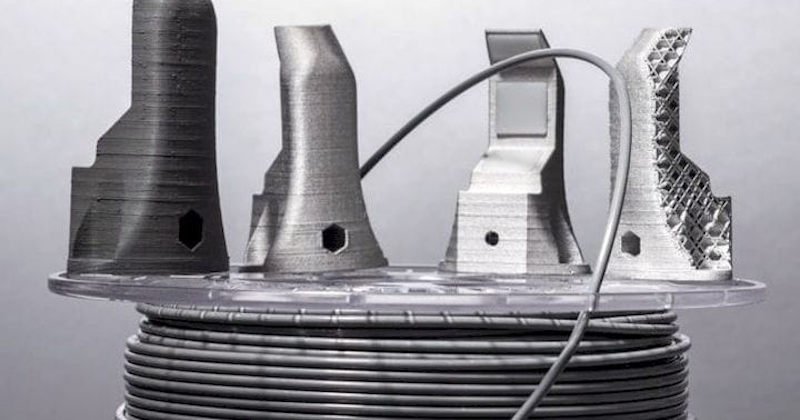
Best metal 3D printer filaments
We recommend the following ranges of metal filaments:
- Copper PLA: available on Matterhackers here / Dynamism here / Amazon here
- Bronze PLA: available on Matterhackers here / Amazon here
- Silver metallic PLA: available on Dynamism here / Matterhackers here / Amazon here
- Stainless steel PLA: available on Matterhackers here
Advantages and Disadvantages of metal filaments

Advantages of metal 3D printer filaments
- Cost: Pure metal printing means investing in a specialist metal 3D printer likely to cost over $100,000, with metal 3D printer filaments costing just a fraction of that. Another viable option would be to use a metal 3D printing service. Costs will be dependent on your specific project. However, like any service, it will still be more expensive than using your own 3D printer and metal filaments.
- Options: There exists a range of metals to choose from at a range of concentrations, all of which can give various properties to your prints. They can feel heavy or light, solid or thin, come in a range of colors, and can even be magnetic!
Drawbacks
- Droopy Bridging and Overhangs: Although the weight of metal filaments can be desirable, this also makes it unsuitable for any print that requires bridging or overhangs. In these cases, the weight of the molten material will cause it to droop, potentially ruining the final shape of a print.
- Fragile: Care must be taken to account for the material’s fragility. Final prints will be brittle, making the material unsuitable for any load-bearing object. Common metal objects such as mechanical components or jewelry would simply be impractical to print, as the material would likely break with limited use.
- Abrasive: Metal filament is abrasive, owing to the metal powders within. Although it will extrude through an unmodified 3D printer, some upgrades are recommended to ensure that the metal filaments don’t quickly wear down its parts.
Tips to get the best results from 3D printing metal-filled filaments
The main appeal of metal filaments is its ability to extrude through a conventional printer without modification. Although this is true, the following hardware and considerations could make your prints more likely to succeed, and your printer last longer.

- Consider upgrading to a wear-resistant nozzle: Most budget 3D printers ship with a brass nozzle as standard. Although suitable for polymers, the abrasiveness of metal filaments can wear away the relatively soft brass very quickly. To avoid this, we recommend upgrading to a hardened steel nozzle.
- Consider using a bigger nozzle: Although standard 0.4mm nozzles will work, metal filaments can clog these nozzles with extended use. If you intend to run your printer for long printing sessions, consider using a 0.5mm or 0.6mm nozzle.
- Avoid printing with bridging or overhangs: Metal filaments are significantly heavier than filaments like ABS or PETG. Although this can add a desirable weight to final prints, it also makes the material perform poorly when bridging or printing overhangs, with the weight of the molten filament causing it to droop.
- Avoid sharp bends in the filament path: As metal filaments are so brittle, they will tend to snap or crack while printing if the path between your spool and extruder has too many sharp bends. These breakages will degrade both the strength, and finish, of your final print. Although you could replace your entire printer to one with a straighter filament path, there are alternative and less expensive methods.
- Consider changing where the filament spool is mounted: Exactly where the straightest path is will vary from printer to printer. However, this is commonly found by mounting the spool on top of the printer. Another method, that can be used independently, or alongside the above, is upgrading your filament guide tube to one that is stronger and more rigid, limiting the potential bend in the filament path.
Applications
Ironically, metal filaments are rarely used as a cheaper alternative to pure metal printing. Despite looking and feeling like the real thing, its fragility prevents it from having similar applications.
Instead, metal filaments are mainly used to print objects that don’t require the strength of real metal but do need to emulate it. Most commonly, this takes the form of ornaments, costume accessories, and museum replicas.
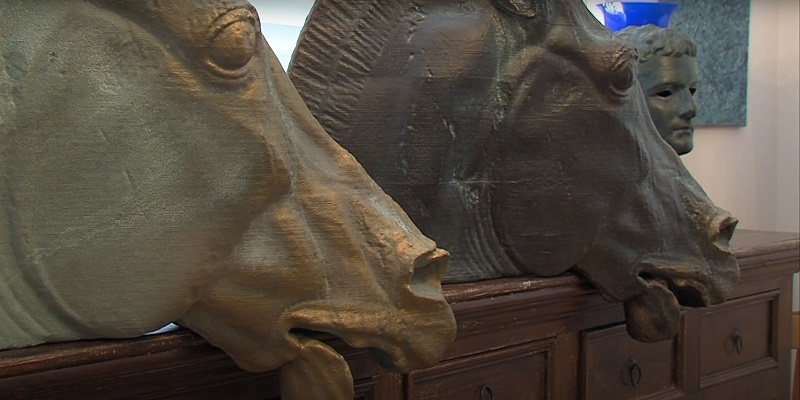
Metal 3D Printer Filaments: Environmental Impact
As metal filaments can have various compositions, its environmental impact will depend on exactly what mixture of polymer and metal you’re using. However, a useful picture can still be painted whilst speaking generally.
Will Metal Filaments Biodegrade?
PLA, the most common polymer used in metal filaments, is completely biodegradable. However, it degrades slowly, potentially taking 80 years to degrade in an open environment.
Likewise, some metals such as tin and aluminum will completely biodegrade. However, this process is also slow, with soda cans potentially taking 100 years to completely rust and degrade. Additionally, more common metals used in metal filaments, such as steel and gold powder, are inert, and will simply never rust or biodegrade.
Although these factors present metal filament as an environmental disaster, they are somewhat redeemed by being almost entirely recyclable.
We’ve known how to reshape and remold metal since antiquity. Additionally, although PLA is difficult to recycle with other plastics, it can be ground down and reconstituted back into filament.
The challenge then isn’t whether both elements are recyclable, but rather, can these composite materials be separated and recycled in an efficient manner?
Recycling Composites

In most cases metal and plastic must be separated to be recycled. As metal exists as a powder within metal filaments, it cannot be separated using conventional methods such as screens and magnets.
Instead, these composites usually have to be ground down into powder and then separated using either chemicals or a centrifuge.
Although this is certainly possible at specialized facilities, these additional steps make recycling composites complex and energy intensive, prompting most recycling centers in the US to not bother processing them.
In practice, this means that although metal filaments are recyclable, putting them in the recycling bin is unlikely to lead to them being repurposed. Instead, they will either be discarded into landfill, or end up contaminating and potentially ruining a batch of clean recycling.
This brings into question the environmental viability of metal filaments. By degrading so slowly, and being complex to recycle, any discarded metal filaments are likely end up either in landfill, or the environment.