
The Myths of Metal Printing (Strength, Cost, Geometric Limits)

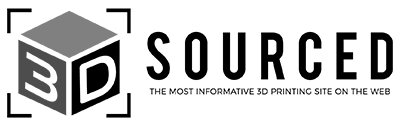
At 3DSourced we’ve covered everything 3D printing and 3D since 2017. Our team has interviewed the most innovative 3D printing experts, tested and reviewed more than 20 of the most popular 3D printers and 3D scanners to give our honest recommendations, and written more than 500 3D printing guides over the last 5 years.
This post was written by Eric Utley, an applications engineer for Protolabs in North Carolina
Most people who delve into printing in metal tend to have at least some experience printing with plastic. While some of those learnings translate, others do not.
So, the big question is what techniques can move from desktop 3D printing to more advanced 3D metal printing processes?
While there are many 3D printing technologies that can print in metal, our focus will be on DMLS (direct metal laser sintering), which prints parts in metal by selectively melting metal powder with a laser.

Similar to most desktop 3D printers, DMLS requires scaffold-like structures to support the part during the build. With desktop printers these supports act to prevent parts from collapse due to gravity during the print.Â
In metal printing, however, these serve an additional purpose. During the print, the metal parts undergo continuous cycles of heating and cooling, and this causes the material to contract and expand.
The supports act to fixture the features in place and resist the effects of thermal expansion and contraction. Because of this, the requirements for supports are more stringent in metal printing, compared to desktop printing.Â
Luckily, a lot of the same principles used in desktop printing to avoid supports apply to metal printing. For example, for most materials and processes, surfaces 45 degrees and steeper do not require supports. Also, using self-supporting structures such as arches provide a fantastic way to avoid unnecessary support structure.
Myth 1: You Don’t Lose Metal Strength

Most desktop 3D printers use FDM technology, which extrudes material layer by layer. While these printers are relatively inexpensive to manufacture with (a plus if you want to print on the cheap), they can create parts that are weak at the layer boundaries. This can cause parts to delaminate and break along layer lines. Most metal printing technologies do not have the same issue.Â
DMLS prints parts in metal by sintering the powder with a laser. With each pass, the laser remelts the layer below, allowing the layers to meld more consistently.
Because DMLS uses powdered metals, many people assume that the material is porous or partially dense, but that’s not the case. Actually, the powder is melted to a fully liquid state before merging with new powder during the printing process.
Metal printed parts using DMLS have tensile strengths as strong or stronger than cast metals of the same alloy, even along the Z build direction.Â
Myth 2: No, You Can’t Print Anything

3D printing is known for its ability to produce diverse designs, even allowing for geometric shapes that would be impossible using any other process.Â
However, while 3D printing processes can produce some truly amazing designs, they cannot produce any shape imaginable. In fact, because it has more stringent requirements for supports, a lot of geometries can’t use DMLS, such as organic models similar to trees, or vascular models.
DMLS is also not well-suited for printed assemblies because supports are often needed in inaccessible areas to fuse parts together. Metal printers can also struggle with thick parts with a lot of material. The large cross sections of metal can contract and even crack during the print.Â
The ideal parts for metal printing use the minimum amount of material required and step up gradually to avoid unnecessary support structure.
Myth 3: DMLS is NOT always cheaper than CNC (it depends on the project)

You have two choices when making a part. A process such as CNC machining takes raw material and cuts it away to reveal the part. That’s a subtractive process. 3D printing is an additive process, layering new powder atop solidified powder below to build a part, layer by layer.Â
Read more: CNC vs 3D printing – subtractive vs additive manufacturing
Here’s where things get tricky. The introduction of desktop 3D printers was revolutionary because it meant that plastic parts could be made quickly and cheaply on-site, instead of manufacturing on a CNC mill.
Plus, CNC machines are larger, more expensive, and require more technical expertise than a desktop 3D printer, making them out of reach for many shops. Beyond that, you get a lot of material waste with milling and models have strict geometry limitations.Â

From a plastics perspective, it is almost always true that 3D printing a part is cheaper than milling it by machining, though a milled part is often superior in accuracy, surface finish, and material strength.
However, comparing metal 3D printing with CNC milling of metal is more complex. Some parts are cheaper and higher quality if machined, while others are better suited for metal printing.
The biggest indicator is complexity. In general, metal printing makes sense for highly complex designs and machining works best for simpler designs, both in terms of cost and quality.Â
Interestingly, some parts may require both processes, first being 3D printed, then with critical features added via secondary machining—something to think about.
Related posts: