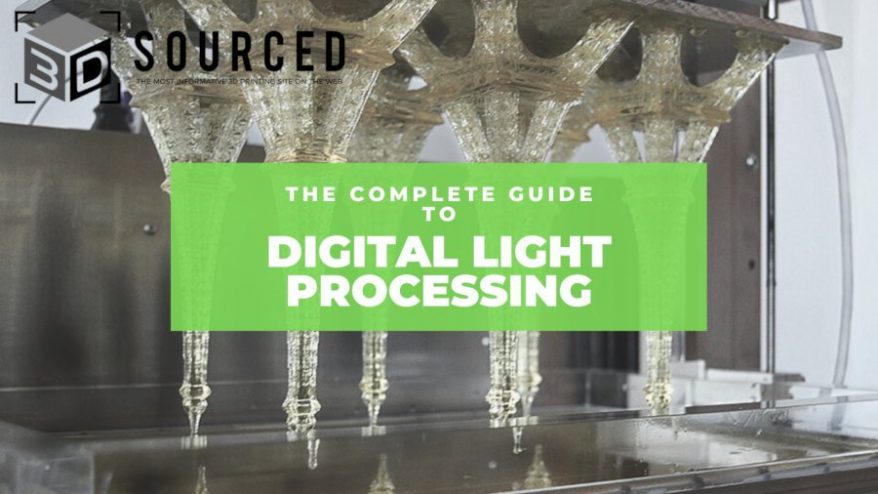
The Complete Digital Light Processing (DLP) 3D Printing Guide
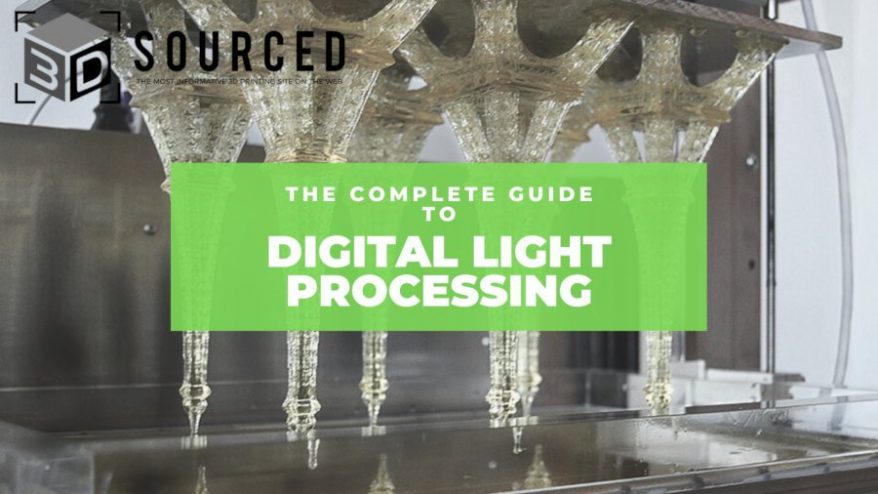
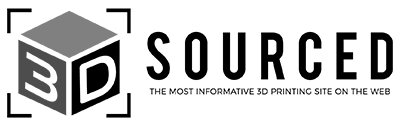
At 3DSourced we’ve covered everything 3D printing and 3D since 2017. Our team has interviewed the most innovative 3D printing experts, tested and reviewed more than 20 of the most popular 3D printers and 3D scanners to give our honest recommendations, and written more than 500 3D printing guides over the last 5 years.
Digital Light Processing technology is one of the most interesting 3D printing technologies out there. It’s also the only one to achieve mainstream usage in other industries — the tech is used in most digital cinema projectors.
This guide will explain how Digital Light Processing additive manufacturing works, the differences between DLP and Stereolithography, and applications the technology has. By the end of this guide you’ll know for sure whether this is the 3D printing technology you’ve been looking for, or whether another — such as FDM or SLS — is better suited.
- Check out our ranking of the 15 best resin 3D printers you can buy, including DLP, SLA and LCD 3D printers.
- If you buy a DLP printer, you’ll need the right software to prepare prints. Check out our ranking of the best resin 3D slicers here.
This guide is also part of our FREE 3D printing technologies EBook. You can download it here.
Digital Light Processing 3D Printing Process
Digital Light Processing was first developed in 1987 by Larry Hornbeck — but not for 3D printing. The tech was developed for projectors and for cinema usage well before it’s potential benefits in 3D printing were discovered. Now, over 30 years later, DLP 3D printers are expected to grow over 30% a year in sales according to Business Wire between 2018 and 2024!
The process works by using a projector. This projector cures a photopolymer resin, one layer at a time, curing the selected areas to be solidified according to the 3D printer model and leaving the surrounding areas uncured. Once one layer has been completed, the part is pulled up by one layer height (e.g. 50 microns) and the process repeats again.
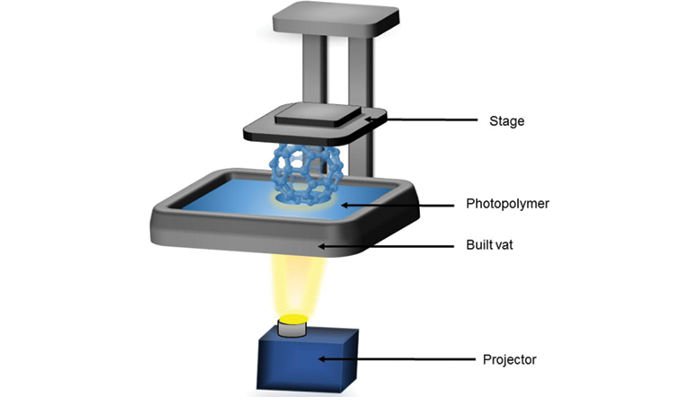
Difference between Digital Light Processing (DLP) and Stereolithography (SLA)
Digital Light Processing is overall very similar to Stereolithography. However, there are subtle differences.
Firstly, the biggest difference between DLP and SLA is that whereas DLP uses a projector, SLA instead uses a UV laser to cure the resin. When printing, the part is still pulled out of the resin layer by layer, but with DLP the whole layer can be created in one singular digital image projection (as can LCD 3D printers), whereas with SLA the UV laser needs to scan the selected area to trace it. This means that Digital Light Processing is faster than Stereolithography in most cases.
Additionally, DLP printers also usually have a shallower vat of resin, so less resin is wasted. This is crucial if you’re on a budget and/or environmentally focused on reducing waste.
Most things are the same however: the same resins work with both types of resin 3D printer, and they have similar applications (more on this later on!).
After Printing Has Finished
After you’ve finished printing your part with DLP, the post-processing is fairly simple. If you’ve used supports, these will need to be removed by placing the part in a bath of isopropanol or similar solvent. Leave the part for a while so the supports can dissolve.
Digital Light Processing Print Quality
DLP prints are above and beyond what is capable from almost any FDM 3D printer. Extremely intricate and difficult geometries can be created using this technology, which is why it has so many applications in 3D printed jewelry and prototyping.
For the same layer thickness, DLP prints are noticeably better than any FDM print, and better than most SLS prints. The surface areas of DLP printed parts are so smooth that is almost impossible to tell that the part was created in layers at all.
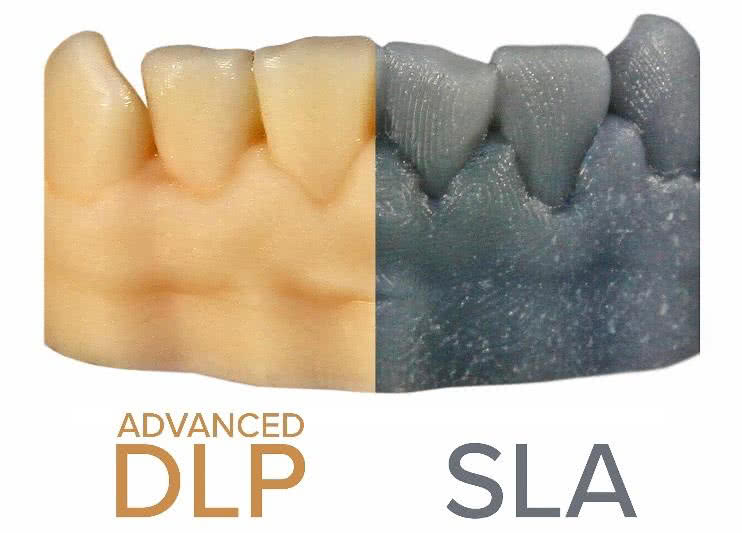
Digital Light Processing 3D Printers and Companies
There are a number of 3D printer companies who compete for the crown of digital light processing 3D printer king. We’ve listed a few of the largest, though there are many fantastic companies we couldn’t list for brevity reasons.
EnvisionTEC
EnvisionTEC make DLP printers specialized in areas such as jewelry, dentistry and for making hearing aids. They use other technologies for some printers, but a core part of their range — such as their VIDA and MICRO PLUS desktop range — utilize digital light processing. EnvisionTEC have been around since 2002 but show no signs of stopping, and now offer a range of machines costing from just a few thousand dollars up to hundreds of thousands of dollars for more industrial machines.
B9Creations
Created by an ex-US Air Force pilot, B9Creations’ innate drive for innovation shows in their printers. Having started from humble roots, B9creations now offer a range of DLP printers such as their B9Creator v1.2, the B9 Core Series, and more. These printers are more consumer focused rather than industrial, so makers at home may be interested in seeing what they have to offer.
Digital Light Processing Applications
There are three main industries than resin models are of particular use. The first is in dentistry, which includes making models for use in orthodontics, teeth molds, and more.
The second is in jewelry in making molds which are eventually used to create solid metal jewelry pieces. We have a guide that explains how lost wax casting 3D printing works which covers this. DLP’s ability to create detailed and intricate pieces is invaluable in this process.
Lastly, DLP is used heavily in creating hearing aids. Hearings aids are one area where, despite its infancy, 3D printing has utterly taken over. 98% of hearing aids are now made with SLA or DLP 3D printers. This is because people’s ears vary in shape and size and a custom sized hearing aid needs to be made for each patient, making 3D printing the most effective production method.
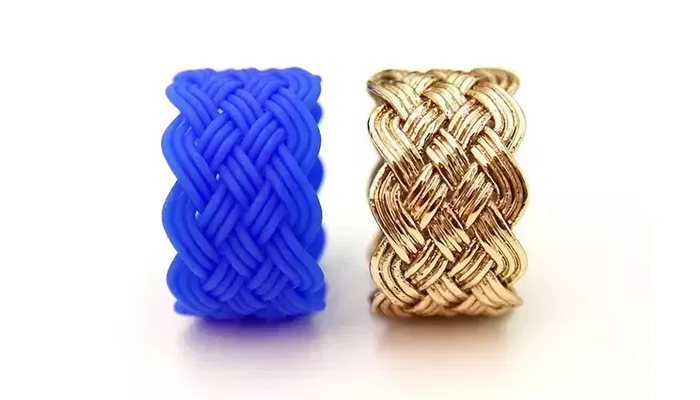
Advantages and Disadvantages of Digital Light Processing
Advantages of DLP
- Very intricate designs — more accurate than FDM or SLS.
- Fast — almost always faster than SLA printing.
- Less running costs than SLA as usually uses a shallower resin vat, reducing waste.
Disadvantages of DLP
- Like with SLA, parts cannot be left out in the sun or they will degrade.
- Parts overall have worse mechanical properties than FDM — they break or crack more easily and are at risk of deteriorating over time.
- More expensive to run than FDM — resins are far more expensive than filaments, and the regular replacements of resin tanks and occasionally print platforms also adds up.